Mini Piling:
Mini piling is a versatile foundation solution used in various construction projects, especially where access is restricted or ground conditions are challenging. Choosing the right materials and following a thorough checklist is crucial for ensuring the success and longevity of mini-piling projects. This article explores the common materials used in mini piling, compares their characteristics, and outlines an essential checklist for executing mini-piling effectively.
Common Materials Used in Mini Piling
Mini piling involves a range of materials, each suited to different site conditions and structural requirements. Below are the most used materials:
Steel
Steel is a general choice for mini piles because of its high strength-to-weight percentage and adaptability. Steel piles can be used in various forms, including tubular, H-section, or solid shafts.
Advantages:
- High load-bearing capacity.
- Durability in challenging environments.
- Flexibility to adapt to different pile lengths and diameters
Disadvantages:
- Susceptible to corrosion in certain environments without protective coatings.
- Greater cost likened to some other materials.
Concrete
Concrete is extensively used in cast-in-situ mini piles or formed piles. To enhance strength, it can be reinforced with steel (reinforced concrete piles).
Advantages:
- High resistance to corrosion.
- Affordable and readily available.
- Customizable to varying load capacities.
Disadvantages:
- Longer curing time for cast-in-situ piles.
- Requires more space and equipment during installation.
Timber
Timber piles, yet less common, are occasionally used in trivial structures or momentary works.
Advantages:
- Eco-friendly and renewable.
- Cost-effective for smaller projects.
Disadvantages:
- Limited load-bearing capacity.
- Vulnerability to decay and pests without proper treatment.
Composite Materials
Composite piles unite materials like concrete and steel to enhance performance. For example, a concrete-filled steel tube joins the compressive power of concrete with the workable intensity of steel.
Advantages:
- Unites the best things of both materials.
- Highly durable and adaptable to complex site conditions.
Disadvantages:
- Higher material and installation costs.
- Complex manufacturing process.
Comparison of Mini Piling Materials:
Criteria | Steel | Concrete | Timber | Composite |
Load Capacity | High | Moderate to High | Low to Moderate | Very High |
Durability | Moderate (requires coating) | High | Low | Very High |
Cost | High | Low to Moderate | Low | High |
Corrosion Resistance | Low without coating | High | Low | High |
Environmental Impact | Moderate | Moderate | Low | Moderate |
Applications | Heavy-duty projects | General construction | Lightweight or temporary | Complex or heavy-duty |
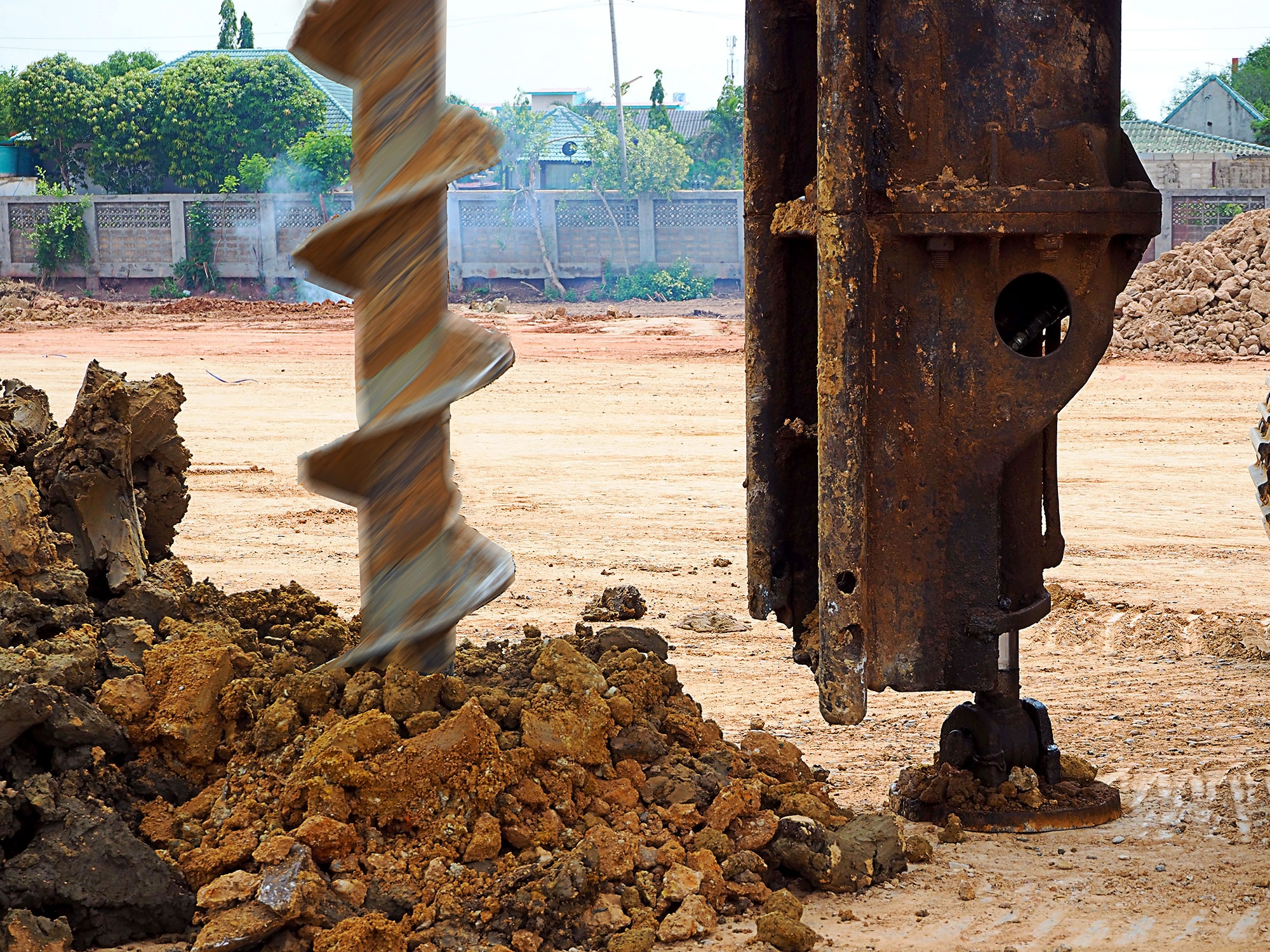
Mini Piling Checklist
Adhering to a detailed checklist before starting a mini-piling project ensures all aspects of the process are addressed, leading to efficient and safe operations.
Site Assessment
- Organize soil analysis to decide ground conditions and bearing capability.
- Identify any underground utilities or obstructions.
- Evaluate access restrictions to determine the feasibility of using mini piling.
Design and Planning
- Choose the appropriate piling material based on load requirements, site conditions, and budget.
- Prepare detailed designs, including pile lengths, diameters, and spacing.
Equipment Preparation
- Select the right piling equipment, such as rigs, hammers, or drills.
- Make sure tools are inspected and in good working form.
- Arrange for necessary safety gear, such as helmets, gloves, and high-visibility clothing.
Material Inspection
- Verify the quality of materials (e.g., steel grade, concrete mix, or timber treatment).
- Ensure compliance with relevant standards, such as BS EN 206 for concrete or BS EN 10210 for steel.
- Store materials in a safe, dry location to prevent damage or contamination.
Installation
- Mark out the pile locations as per the design.
- Monitor the installation process to ensure piles are driven to the required depth or resistance.
- Check for verticality or alignment during the installation.
Quality Control
- Perform integrity tests, such as sonic or dynamic load testing, to verify pile performance.
- Record installation data, including depth, driving force, and material usage.
- Address any discrepancies or issues promptly.
Post-Installation
- Trim pile heads to the correct level and prepare for integration with the structure.
- Dispose of waste materials, such as excess concrete or cut-off steel, in an environmentally responsible manner.
- Check the project to certify all work allies with design terms and safety values.
Selecting the Right Material and Checklist for Accomplishment:
The selection of Mini Piling Oxford material depends on dynamics like project requests, site conditions, and budget. Steel may be ideal for projects requiring high load capacity and flexibility, while concrete suits general construction needs. Composite materials, though costlier, offer superior performance for complex projects.
Meanwhile, the checklist serves as a guide for ensuring smooth and efficient execution, from site assessment to post-installation activities. Following these steps minimizes risks, enhances quality, and ensures compliance with industry standards.
By carefully selecting materials and adhering to a comprehensive checklist, contractors can achieve durable and cost-effective foundation solutions using mini piling. The process not only ensures structural stability but also fosters client satisfaction, setting the stage for successful construction projects. With expertise in mini piling, underpinning, and deep foundation systems, Southern Foundations & Piling is known for its innovative techniques and commitment to structural integrity.